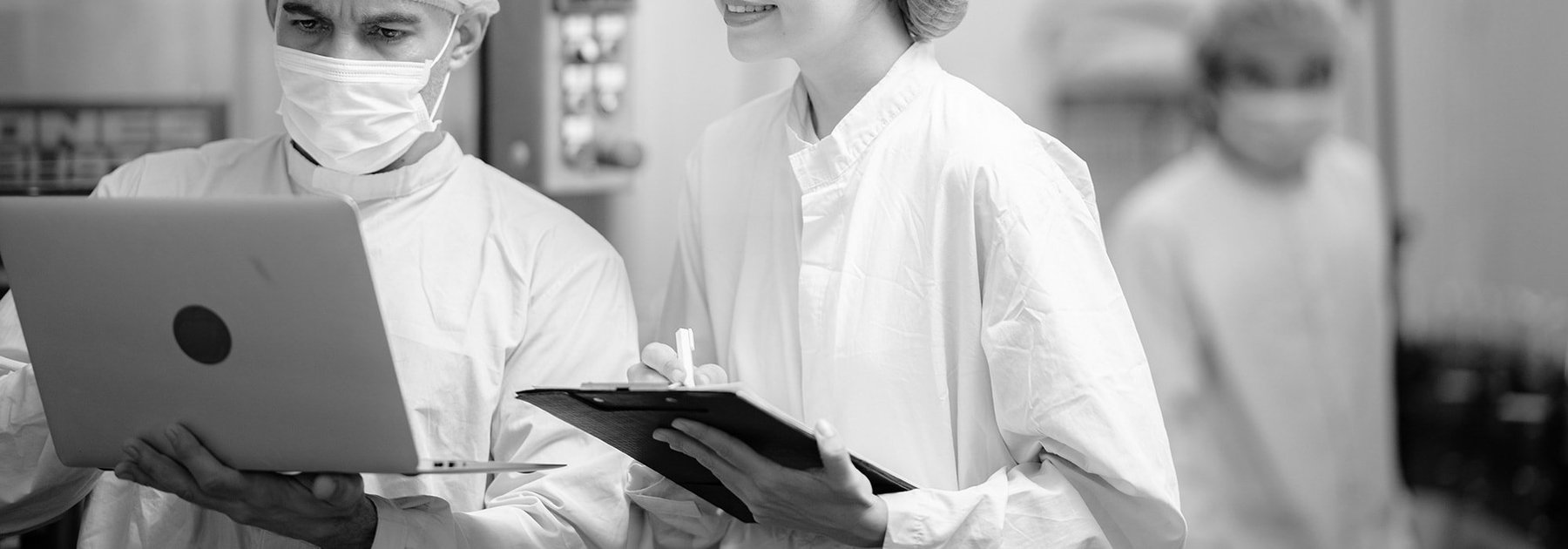
Specialist Consultancy
Delivering and installing your food production solution
Taking the first steps
Sealpac UK and Partners have everything you need to make the entire process smooth and efficient. Whether it is a simple single machine or a complex food production line solution, we treat your installation with the same attention to detail that every customer deserves. Our team have a wealth of knowledge and experience gained from time served in the food industry.
If you need to integrate with existing machinery, our experienced project team and consultants will guide you through best practice to get the most from adding to an existing production line to achieve optimum performance with seamless integration.
We work hand in hand to get to know your processes and the team behind it so we can create a tailor made solution to fit both technically and within your budget and delivers savings right across the board, from efficiencies in production to reduced downtime. And better yet, it’s all backed up with the ongoing class leading support required after installation.
Bringing the concept to reality
- It starts with a visit from our project design engineers to discuss the specification and plan the installation in your factory.
- The machine is designed in to the working area along with agreeing orientation, services, speeds, product and packaging testing and an installation time plan.
- When the order is ready, our project team and engineers carry out testing with you before delivery to ensure the machinery is ready for installation. This helps to keep the disruption of installing in the factory to an absolute minimum and ensures we hit the ground running.
- On delivery we meet you at the factory to offload the machine and get it in place. From there, our engineers take over and install the machinery before commissioning.
- After commissioning, we train your people and can arrange additional support for the first days in production, ensuring your team are confident to continue with the day to day running of the production line.
On completion of the 5 steps, the engineering team will discuss the long term plan to keep your new machine running for years to come with a choice of tailor made spare parts and service contract packages to suit your needs. Support is also on hand whenever you need it and just a phone call away.
A strategic approach
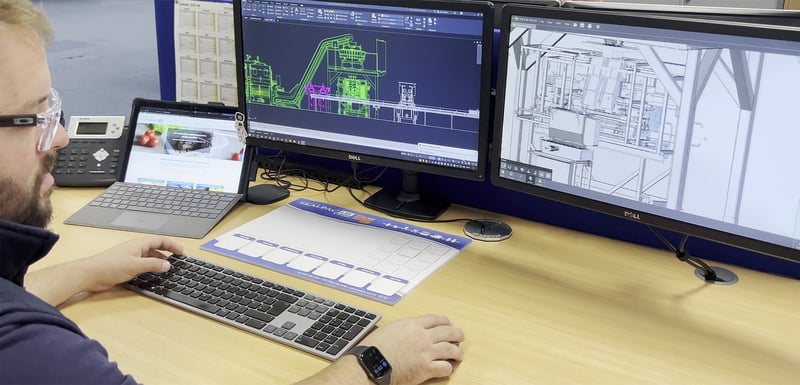
The right tools for the job
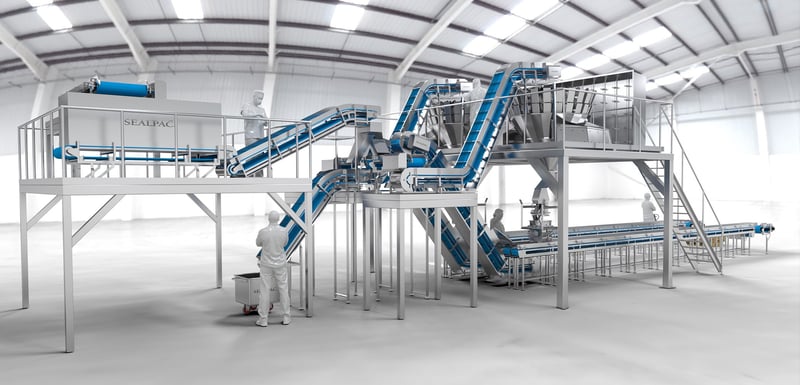
Features and benefits
Let us take the strain
Best practice
Optimum performance
Machines for the long term
-
Case Study
Successfully Relocating Packaging Solutions To A New Site For A Poultry Processing Company
Relocating Packaging Solutions In A Poultry Processing Company The Challenge The challenge presented to us involved relocating three A series...
Read the full Case Study -
Case Study
Food safety – Inspection and detection
Automated food quality and safety inspection solutions The Challenge The presence of micro-holes in food packaging is a particularly critical problem in...
Read the full Case Study -
Case Study
Sliced cheese line
Raising efficiency and production The Challenge Between 400 & 500 tons of cheese move through the packaging and production facility. Since the demand for...
Read the full Case Study
Full line solutions
We design and project manage the installation of bespoke machines across the full production line. Our network of partnerships has helped us to expand our range to offer automated full line solutions which are flexible enough to fit around your business needs and respond to a changing market.
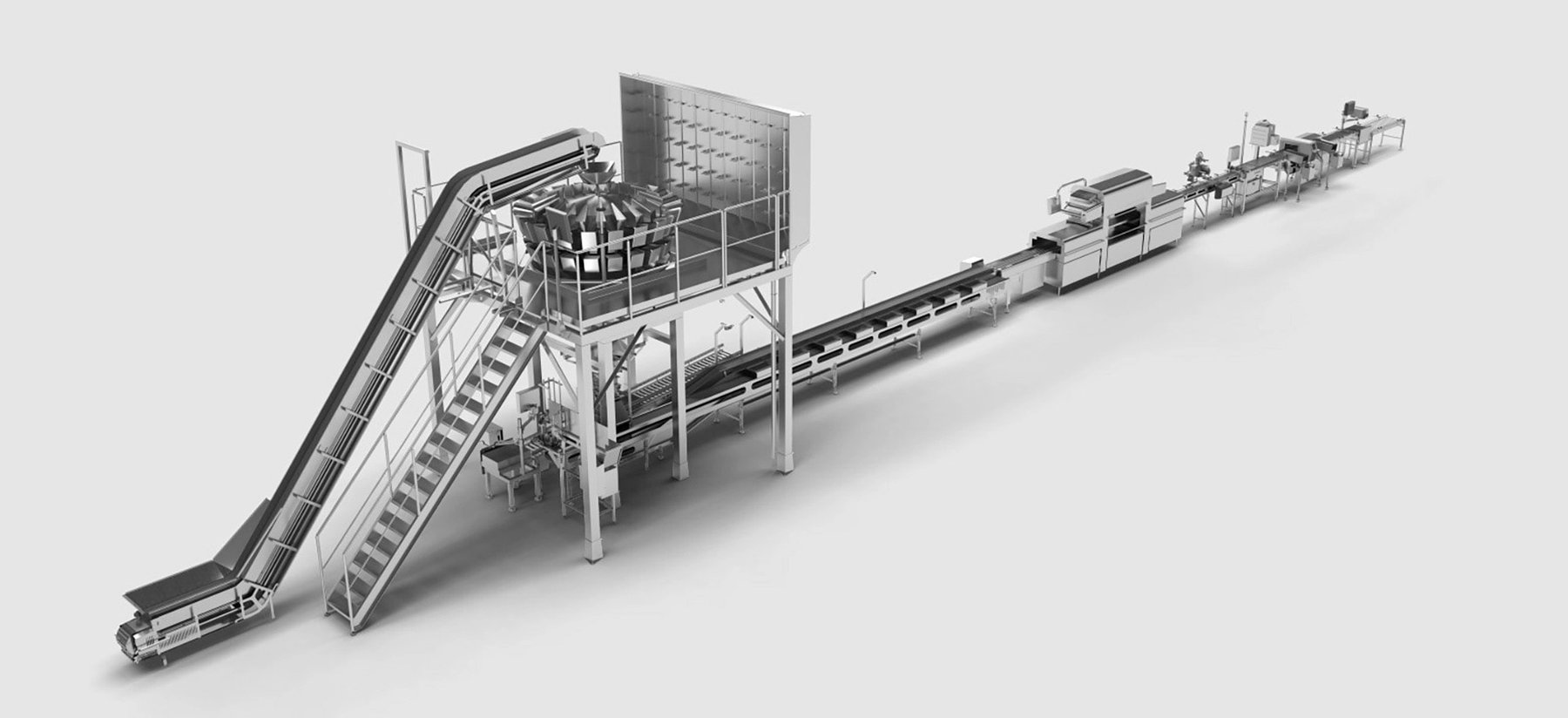
Do you have a project that you’d like to discuss?
Our experts are on hand to help maximise the efficiency of your line. Let’s see what we can do for you.