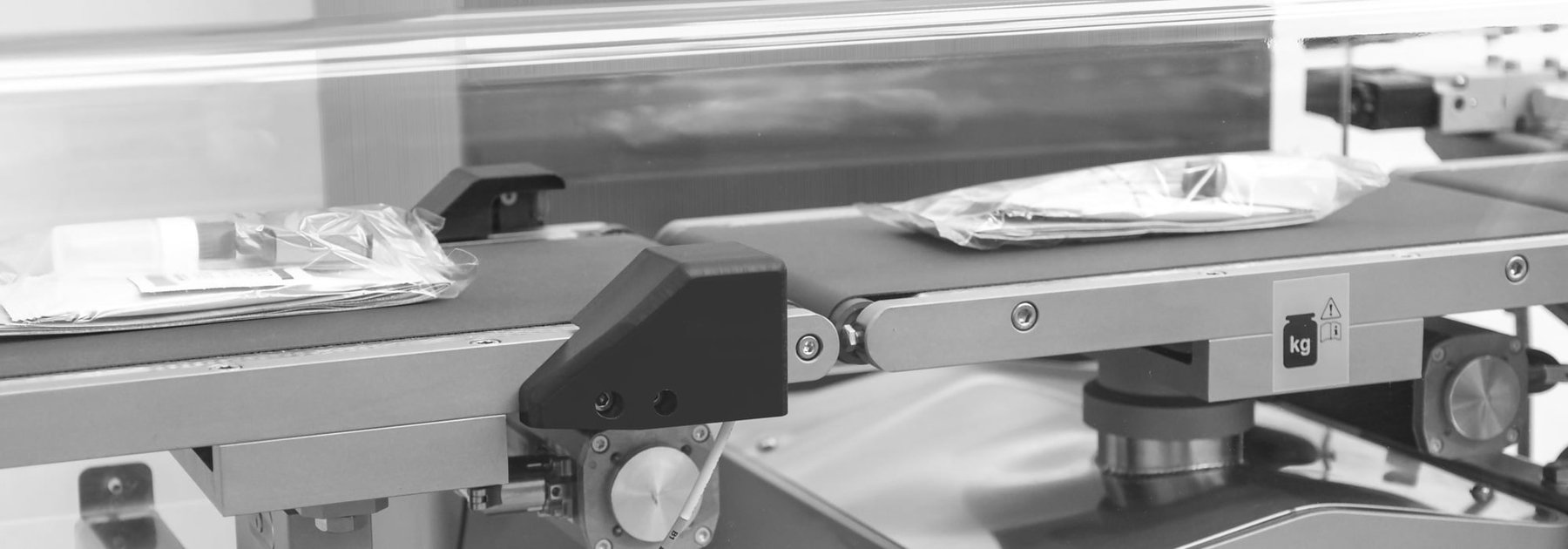
Quality Control & Inspection
Guarantee a quality product every time with fast and reliable inspection in real-time with total traceability
Ensuring your products are of optimal quality before they reach supermarket shelves is key to maximising production efficiency whilst avoiding costly product recalls and damage to your brand’s reputation. Bringing increased automation to the production process often means an increase in speed where manual checks are costly and not enough to spot every product defect.
Increased productivity
The verification of your products rejected from the line due to defect, foreign bodies, wrong or missing labels and over and underweight allows you to intervene on the process in real-time, reducing risks and recovering productivity.
Less waste
Total check for crates and cases
Space saving “all in one” systems
ALL-IN-ONE Food Inspection Systems
An innovative solution, unique on the market, including all the needed inspections in one single system. Simply identify your inspection requirements, Antares Vision Group - ALL-IN-ONE will meet them all thanks to our wide range of technologies, integrating multiple checks in one compact machine.
Find out more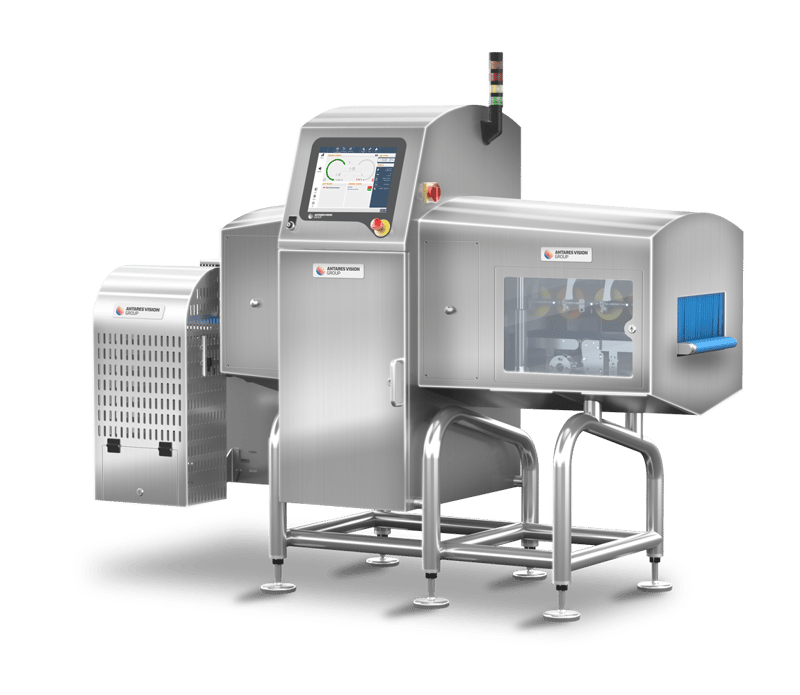
Label and Code Inspection
Knowing you have the right information on your packs is critical to consumer safety and your brand reputation. Vision systems by Antares Vision Group check the quality of labels (alignment, positioning, items or brand, languages, etc.), codes (expired data, lot number, barcode, Data Matrix, QR code) and the correlation between single products and secondary packaging.
Find out more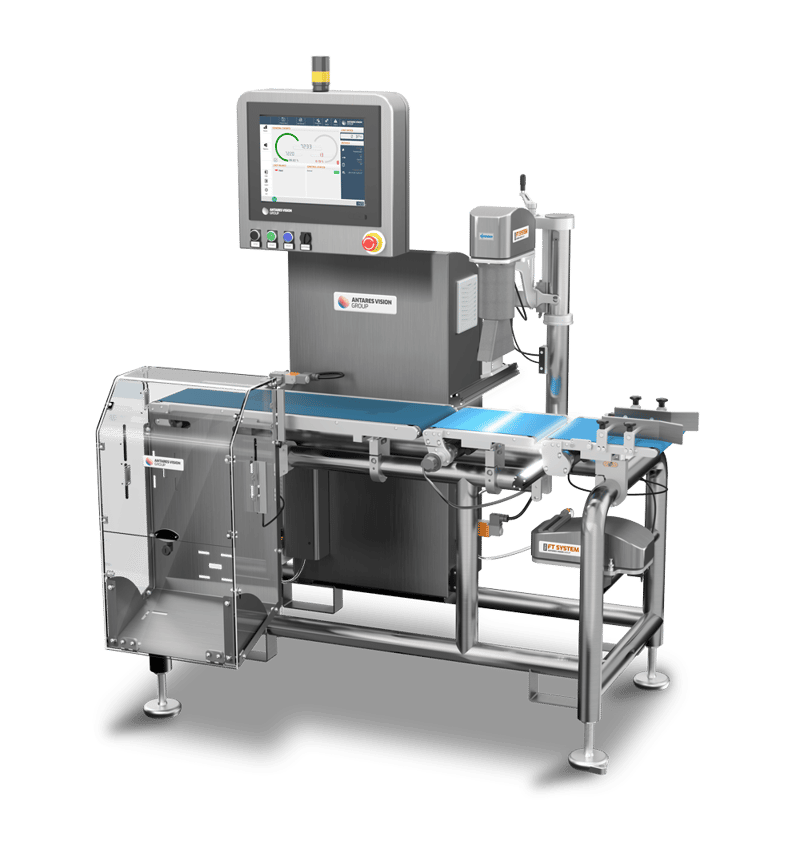
Leak and Seal Inspection
An innovative application of IR spectroscopy to detect inline holes and microholes in packages by checking for CO2 leakage (for MAP products), alcohol or a specific flavour. In-line sealing area inspection to detect the presence of products and physical contaminants. Available for transparent or coloured film and packaging through hyperspectral or artificial vision technologies.
Find out more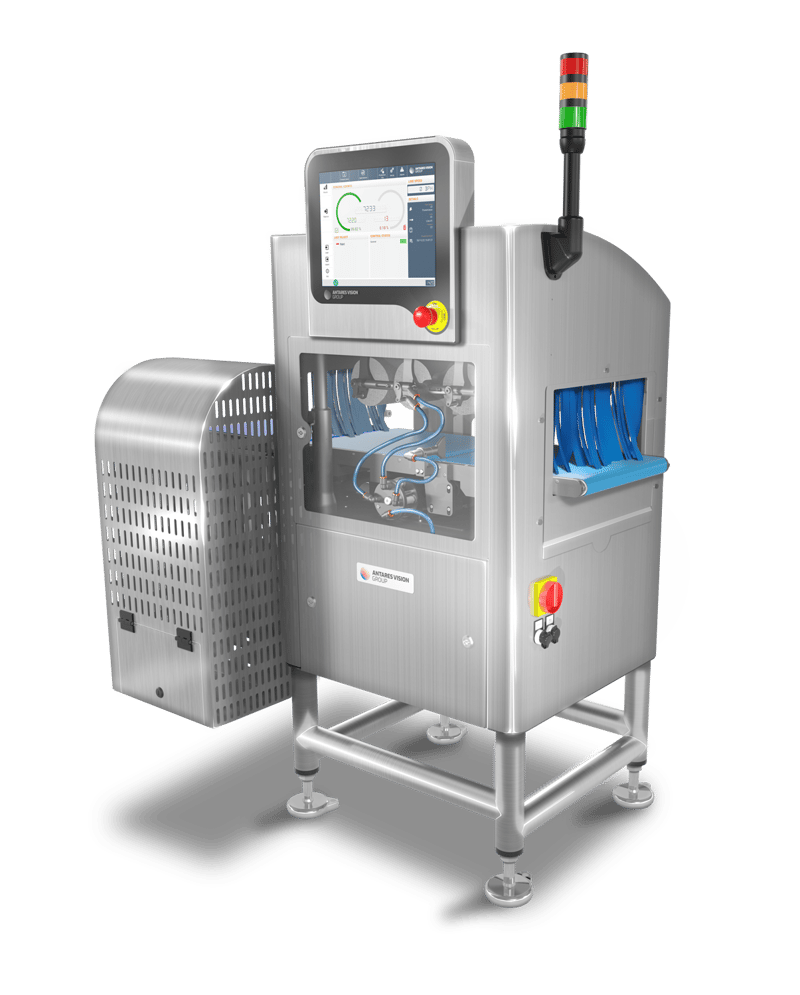
X-Ray Food Inspection
Antares Vision Group inspection technology uses X-rays to identify foreign bodies of different densities. It generates a grayscale image of the product and the software, through a multi-algorithm analysis, highlights contaminants and rejects non-compliant items.
Find out more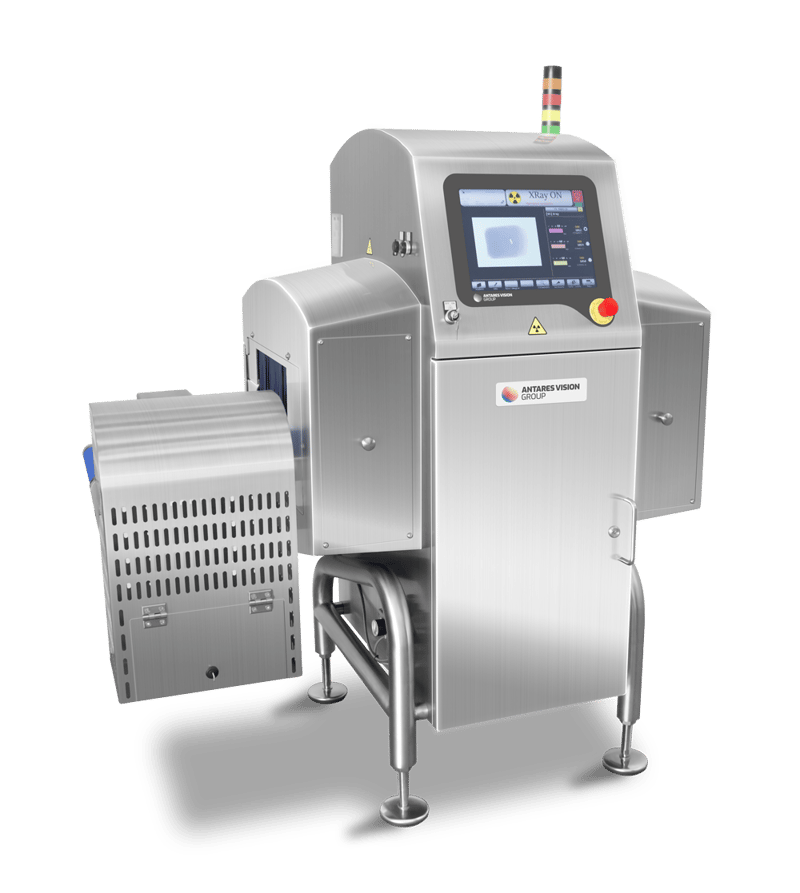
Metal Detector
By detecting the presence of metal contamination, Antares Vision Group metal detectors for food provide effective protection against ferrous and non-ferrous metals (aluminium, stainless steel, etc.) and guarantee customer safety.
Find out more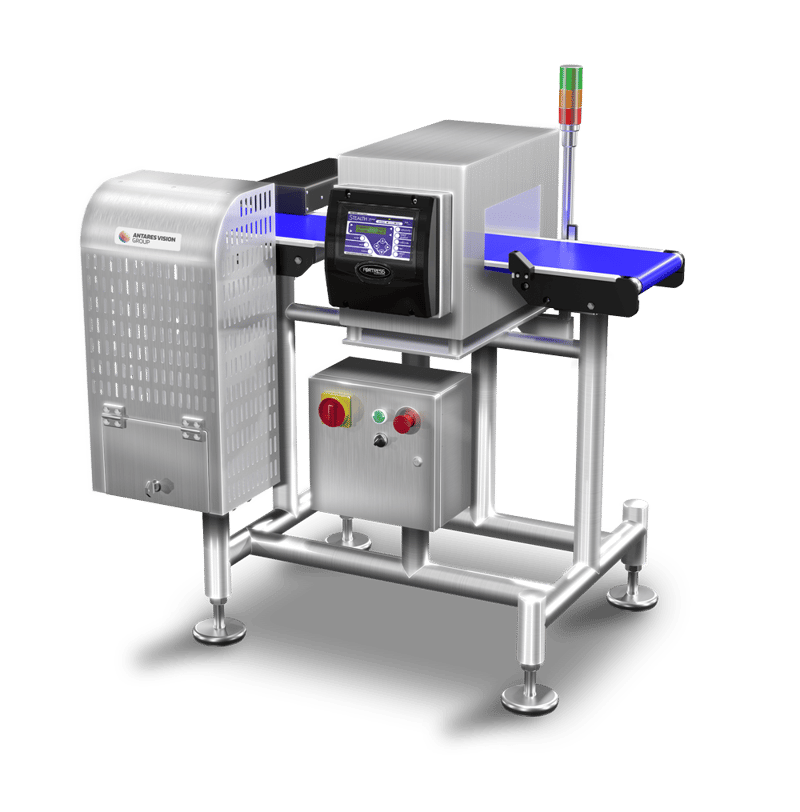
Checkweigher
Antares Vision Group checkweighers are high-precision measuring instruments designed to check the weight of individual products. On board reporting and networking allows you to see your line efficiency in real time and guarantees the right weight for the consumer.
Find out more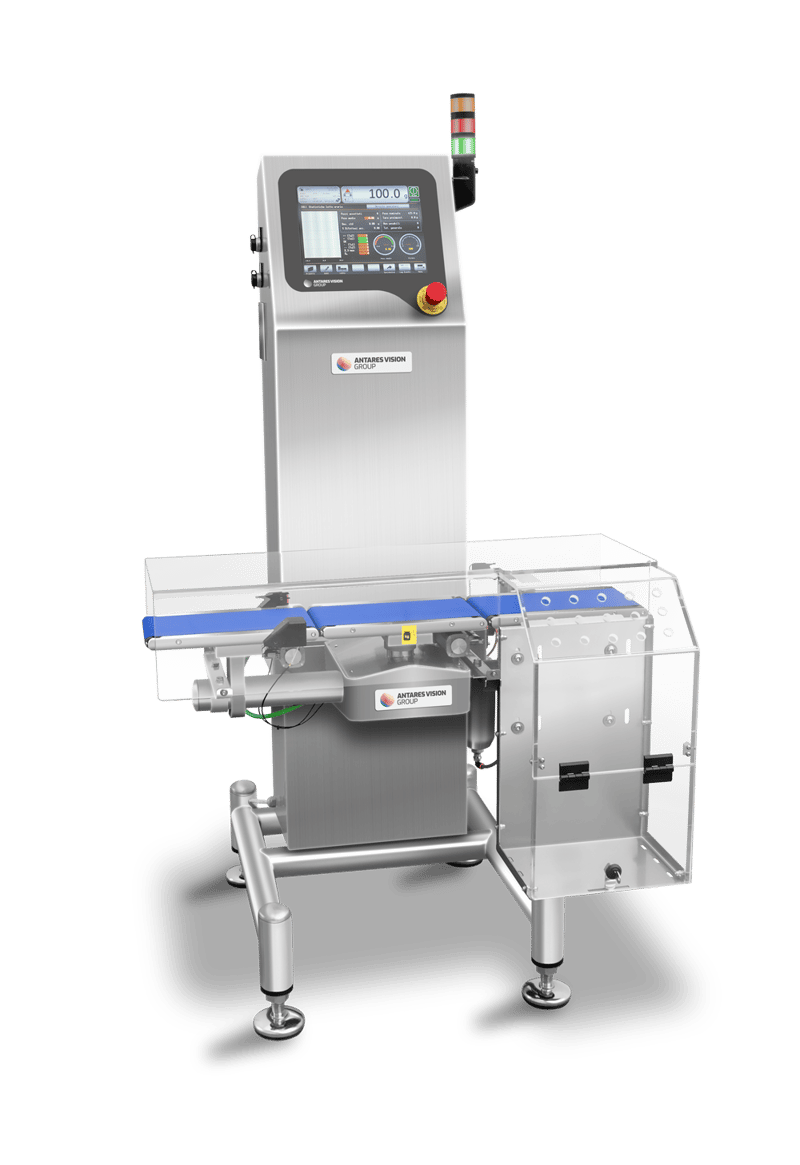
Combi Inspection Systems
Browse from a range of Antares Vision Combi systems that integrate multiple inspection functions, including X-ray, metal detection, and checkweighing, in a single compact unit. These versatile solutions enhance product safety and quality, handling various product types while optimising efficiency and ensuring compliance with industry standards.
Find out more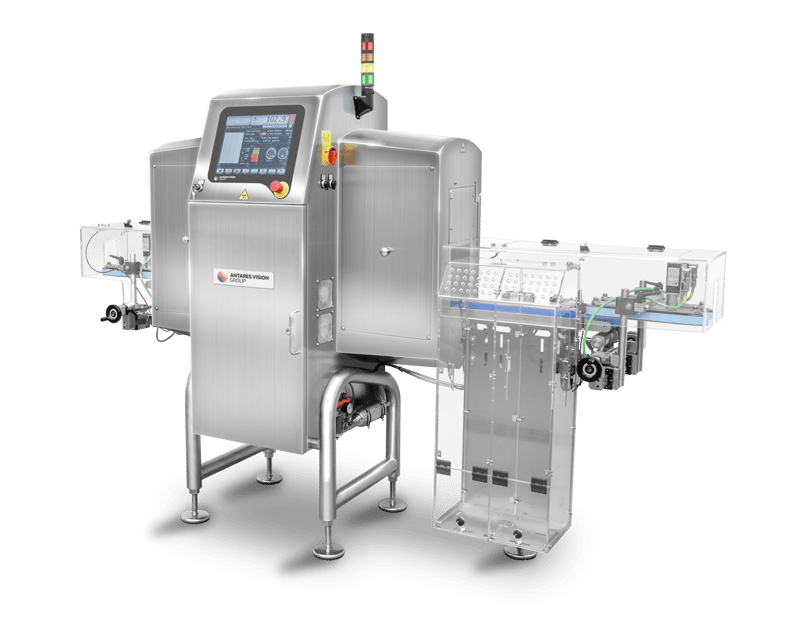
Microwave food inspection
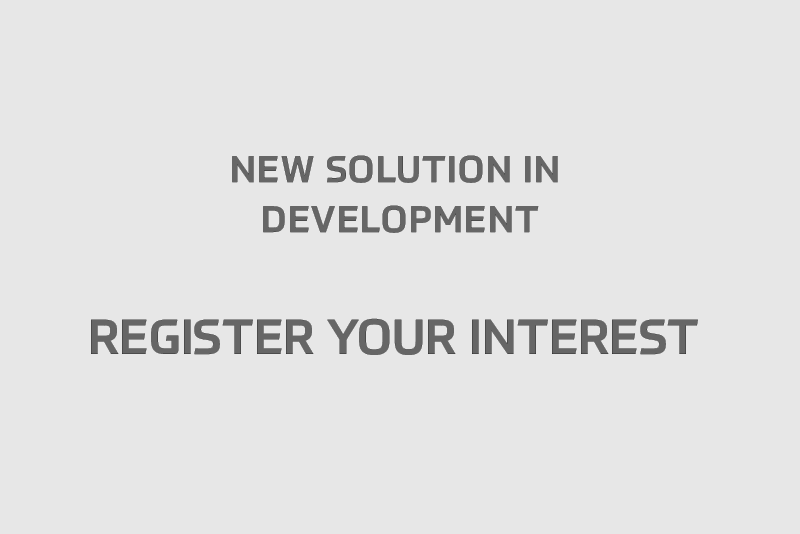
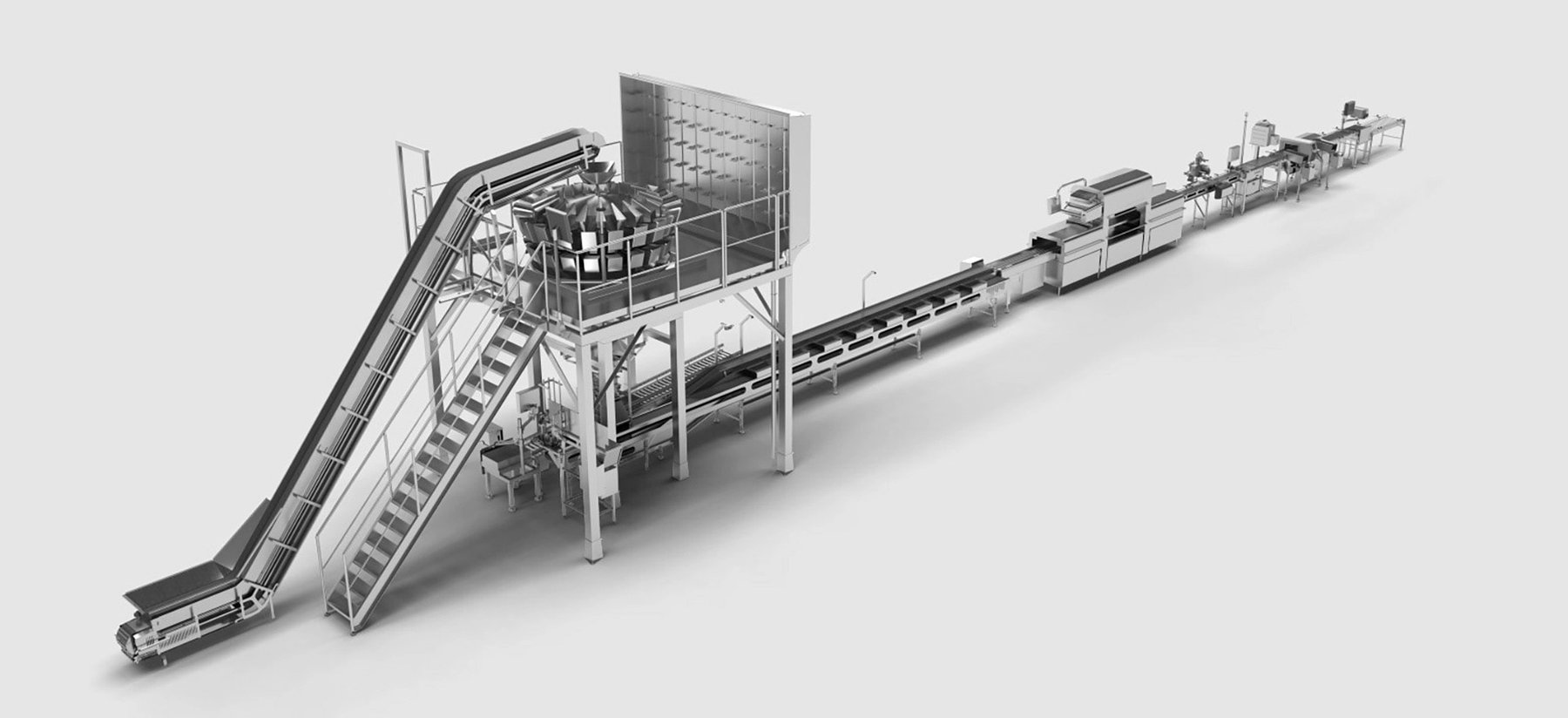
How can you benefit from our expertise?
Whatever your production line requirements, we have the expertise that can really make a difference to your overall efficiency and operating costs. Get in touch with us today to arrange a consultation with our expert team and let’s explore the possibilities.
Full line solutions
We design and project manage the installation of bespoke machines across the full production line. Our network of partnerships has helped us to expand our range to offer automated full line solutions which are flexible enough to fit around your business needs and respond to a changing market.
-
Case Study
Food safety – Inspection and detection
Automated food quality and safety inspection solutions The Challenge The presence of micro-holes in food packaging is a particularly critical problem in...
Read the full Case Study